The Challenge
Purchasing used to be made based on min/max parameters that had to be manually adjusted
Prior to the AGR implementation, Olís was spending too much time managing over 10.000 of SKUs
Stock levels were too high and service levels could easily be lifted
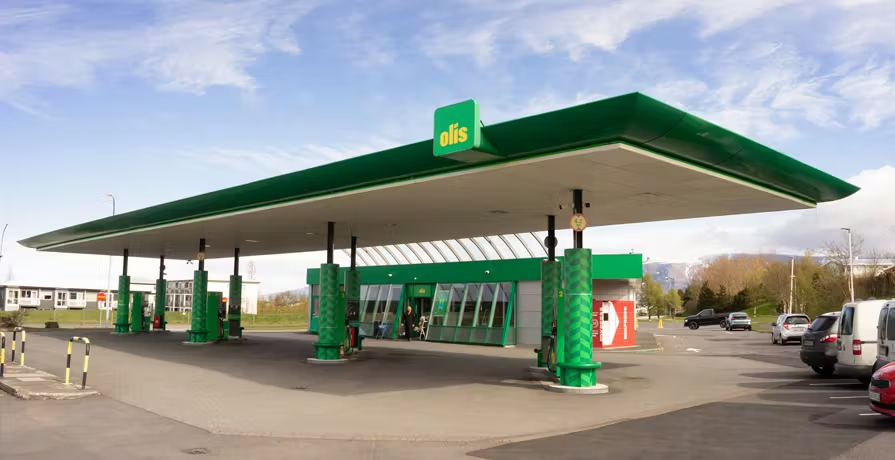
The result
- 30% increase in turnover ratios
- Timesaving in the purchasing process. Increased service levels
- Increased management overview
- More cash for the business
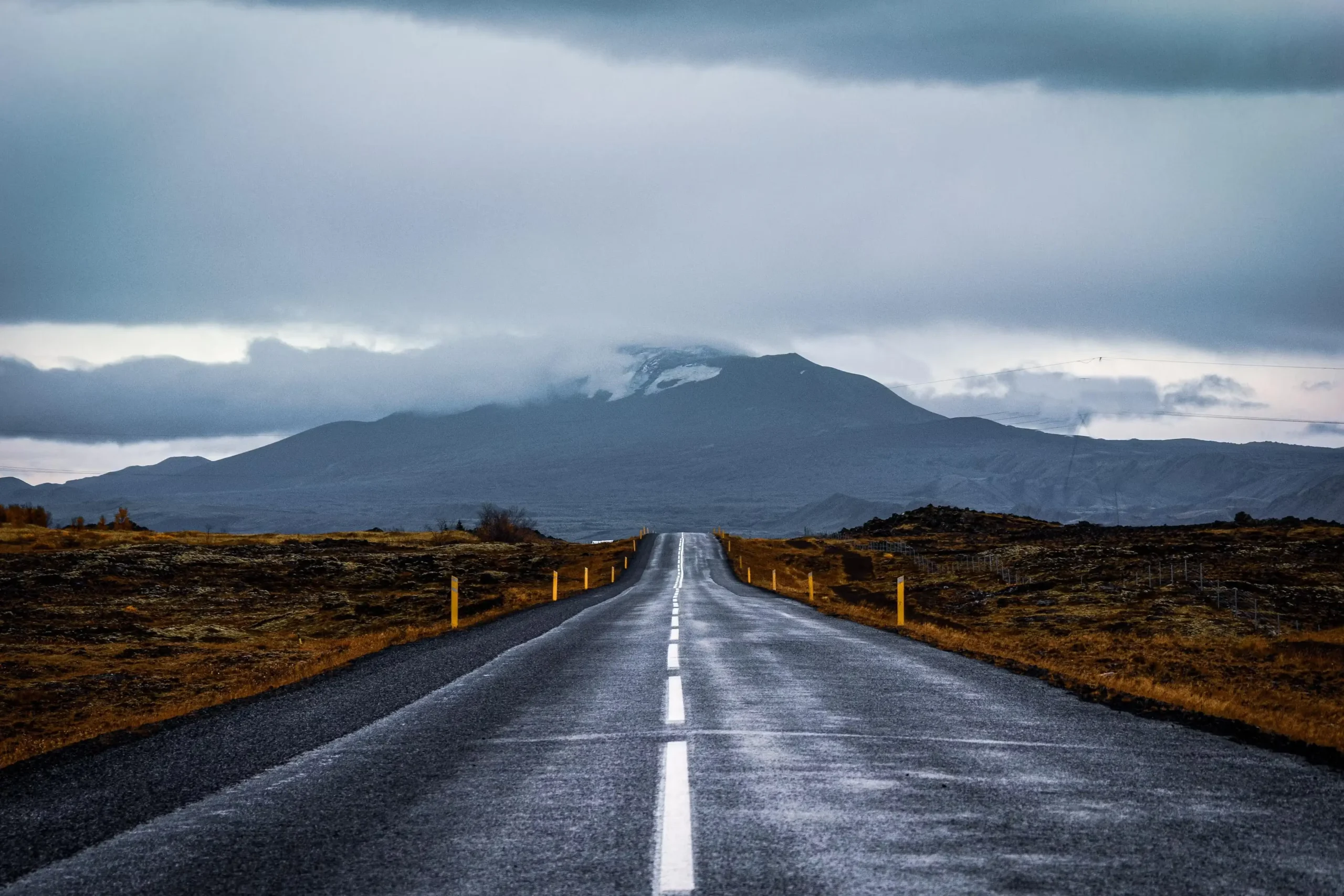
“AGR has helped us increase turnover ratios by 30% and improve service levels while minimizing work in the buying process. We are currently implementing the system in all our retail outlets.”
- Olís
- Sigurdur K. Pálsson, Purchasing Manager, Olís Ltd.
Supply Chain Challenge
Olís is one of Iceland’s largest corporations, serving its customers with fuel and related products. Olís runs over 60 service stations throughout the country. Besides traditional items for vehicles, the stores also feature hot and cold snacks, chilled food and drinks, cleaning products, toys and goods needed when travelling. In total, over 10.000 SKUs are managed by Olís in several distribution and service centres. Items are distributed daily to over 60 service station around Iceland. Prior to the implementation of AGR, Olís had been doing the demand and inventory planning with a DOS-based ERP system. Forecasting was based on average sales figures from past periods and safety stock levels were determined by using weekly sales figures.
Olís chose to invest in AGR to improve its demand and purchase planning procedures. “We decided to buy the system after carefully evaluating its potential benefits. It was clear to us that AGR would improve our purchasing procedures dramatically. AGR’s excellent reputation also helped us in the buying process,” says Sigurður K. Pálsson, Purchasing Manager.
Automation of inventory planning tasks
AGR has been implemented in Olís’ distribution centres. It automatically selects the best-fitting forecasting method and creates automatic order proposals. Time-consuming tasks have been eliminated from the ordering process. What used to take days now takes only hours. Exception reports give special attention to extraordinary items.
Easier implementation of Microsoft Dynamics Nav
Olís recently changed its ERP system from the old DOS-based system to MS Dynamics Nav. Historical data was already present in AGR’s database, which meant that the new ERP system could start off fresh without going through the tedious process of mapping data.
Benefits and next steps
“We have been extremely happy with the results, and we are currently rolling the system out to all our service stations. AGR has helped us improve turnover ratios by 30%, improve service levels and save valuable time in the buying process”, says Sigurður K. Pálsson, Purchasing Manager.